Rotordynamics Analysis
Rotordynamic analysis is a specialized field of engineering that focuses on the study and analysis of rotating machinery systems, particularly their dynamic behavior and stability. It involves the investigation of the vibrations, forces, and moments experienced by rotating components, such as shafts, rotors, bearings, and seals.
Key Aspects and Objectives
Rotordynamic analysis combines principles of mechanics, vibration analysis, and fluid dynamics to assess the dynamic behavior and stability of rotating machinery systems. By understanding and controlling the forces and vibrations within these systems, engineers can design, operate, and maintain rotating machinery with improved performance, reliability, and safety.
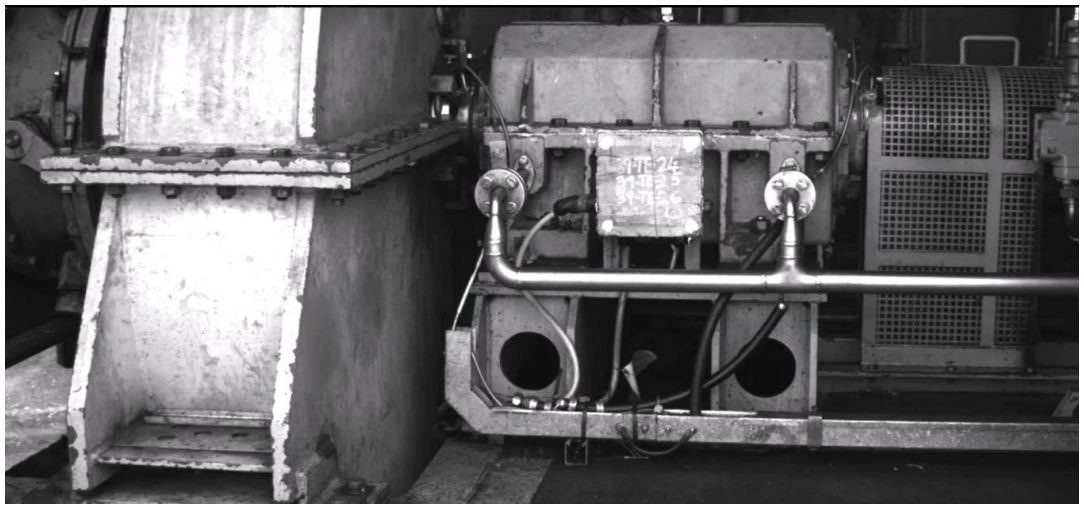
Stability Analysis
One of the primary concerns in rotordynamics is ensuring the stability of rotating machinery systems. Stability analysis involves evaluating the potential for self-excited vibrations, such as whirl or oil whip, which can lead to catastrophic failures if left uncontrolled. Stability margins are assessed to ensure that the system remains stable throughout its operational range.
Natural Frequency and Mode Shape Analysis
Determining the natural frequencies and mode shapes of a rotating system is crucial in understanding its dynamic behavior. Natural frequencies represent the frequencies at which the system naturally tends to vibrate, while mode shapes describe the associated vibration patterns. Analyzing natural frequencies and mode shapes helps identify critical speeds and modes that can influence system performance and potential resonant conditions.
Click here to read more on how experimental techniques could be done to obtain the natural frequencies and mode shapes:
Critical Speed Calculation
Critical speeds are rotational speeds at which the natural frequency of the system matches the operating frequency. It is important to identify and avoid operating near critical speeds to prevent excessive vibrations and potential damage. Calculating critical speeds is a fundamental aspect of rotordynamic analysis.
Rotor Balancing
Balancing is a technique used to minimize the vibrations caused by mass imbalances in rotating machinery. Rotordynamic analysis helps determine the amount and location of unbalance, guiding the balancing process to reduce vibrations and improve overall system performance.
Bearing Analysis
Bearings play a crucial role in supporting and guiding rotating shafts. Rotordynamic analysis involves evaluating bearing characteristics, such as stiffness, damping, and load capacity, to ensure proper functioning and minimize vibrations. Bearing parameters are analyzed to optimize performance and prevent issues like excessive wear or instability.
Rotor Response Analysis
Rotordynamic analysis investigates the response of rotating components to external forces, such as unbalance, misalignment, or fluid forces. This analysis assesses the dynamic behavior and predicts the resulting vibrations, stresses, and deflections in the system. Understanding the rotor response aids in designing robust and reliable rotating machinery.
Shaft Whirling and Stability Control
Shaft whirling refers to the lateral vibrations experienced by rotating shafts. Analyzing and controlling shaft whirling is crucial for ensuring system stability and preventing issues like excessive vibrations, high stresses, or contact between rotating and stationary components.
Case Study
Rotordynamic Analysis of Atomization Air Blower
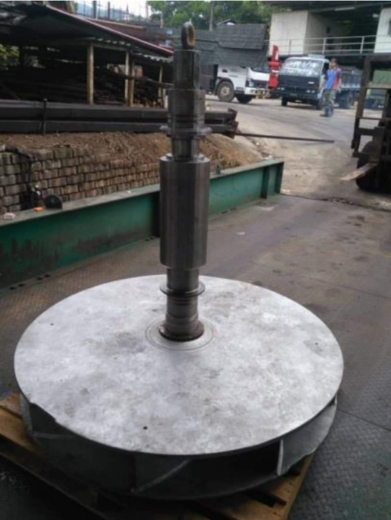
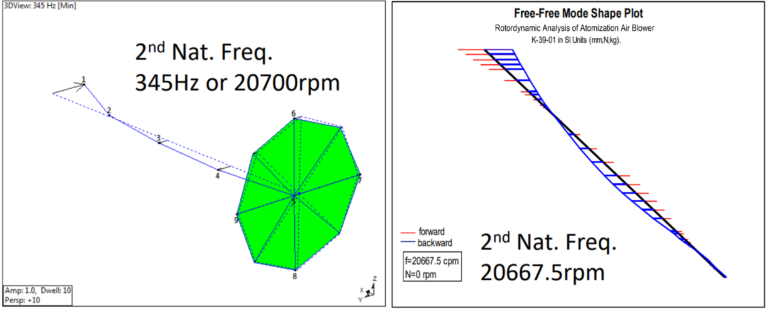
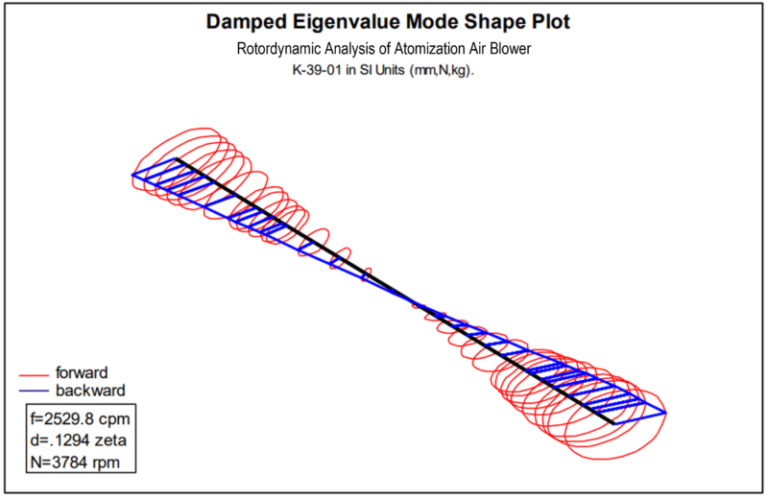
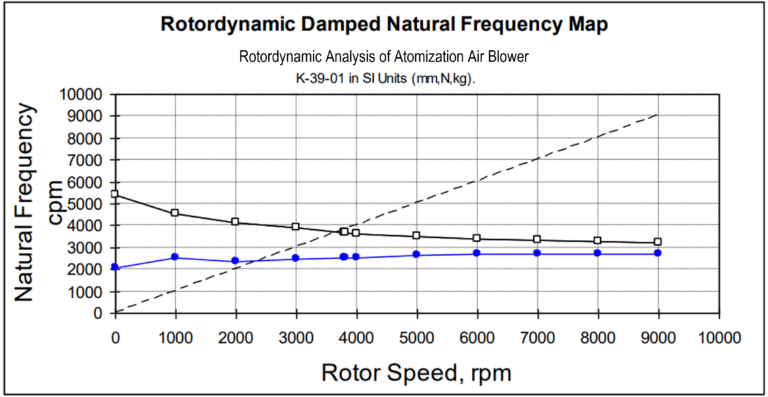